商用车
2022-09-14
重型设备制造商如何应对价格上涨、材料短缺以及实现减排目标?
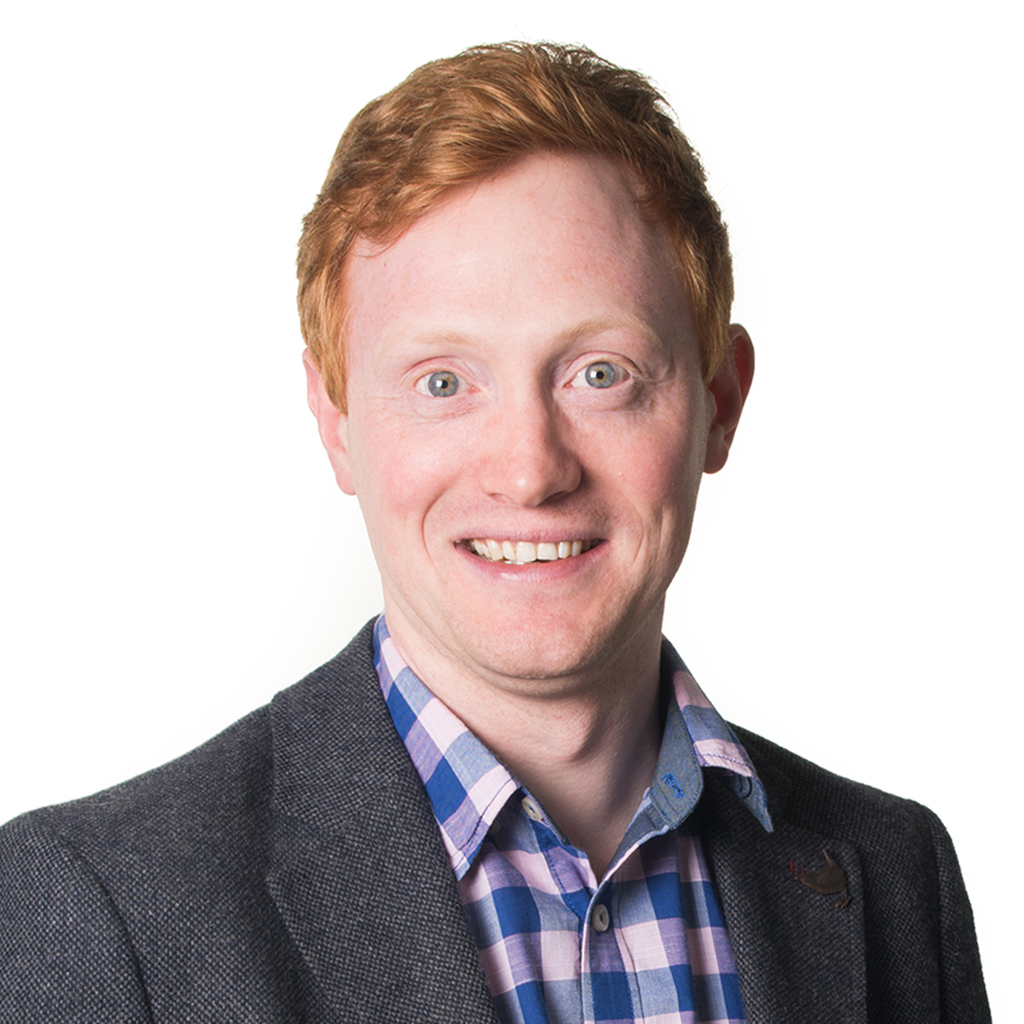
ALASTAIR HAYFIELD
Alastair在规模化、高增长的工业和技术市场领域拥有超过15年的领导研究项目经验。作为商用车辆部门的高级研究总监,他负责电动卡车和公交车、自动驾驶和非道路设备电动化领域的前沿研究。
Heavy Equipment Needs to Go on a Diet
The use of light-weight materials is very common in automotive, helping OEMs and suppliers meet emission and performance goals. Aluminium, carbon fibre, plastics, structural adhesives and more are all a part of the manufacturers’ tool kit when it comes to shedding pounds.
But is the use of light weight and alternative materials a practical choice for off-highway machine builders? It comes with a higher cost, performance challenges and, given the extreme operating conditions for most machines, potentially shortened life expectancy.
All this might change. As the industry slowly awakens to the potential of electrification and is hammered by rising material and fuel costs, will we see off-highway OEMs look at ways to improve efficiency and reduce the use of certain materials?
Does my BOM Look Big in This?
For the most part, there has been almost zero focus on machine weight in the off-highway industry. Whilst soil compaction might be an issue in agriculture, heavy and robust construction machines are typically required from a longevity and balance perspective (large excavators have removable counterweights precisely because they might topple over if they didn’t have them when moving heavy loads). Machinery is also often operated when it is static, meaning that there is no efficiency penalty from having a very heavy machine. However, not all machines stay still and not all parts of machines are static: there are opportunities a plenty for the off-highway industry to tighten its belt and reduce the bill-of-materials (BOM).
A Weigh to Go
Off-highway is, predictably a long way behind automotive when it comes to light-weighting, material substitution and novel manufacturing techniques. To give a few examples from automotive:
The 2013 Range Rover became somewhat of a “celebrity dieter” when it was launched, being nearly half a ton lighter than its predecessor thanks to an all-aluminium chassis. Aluminium is now commonly used in cars for light-weighting.

www.motorauthority.com
(Source: https://www.motorauthority.com/news/1078486_2013-land-rover-range-rover-preview-700-pounds-lighter)
BMW used carbon fibre reinforced plastic (CFRP) for its mass produced i3. Although it is more expensive than steel, it made the chassis lighter (a substantial boon for the electric i3) and the production process versus steel or aluminium is quicker and less energy intensive.
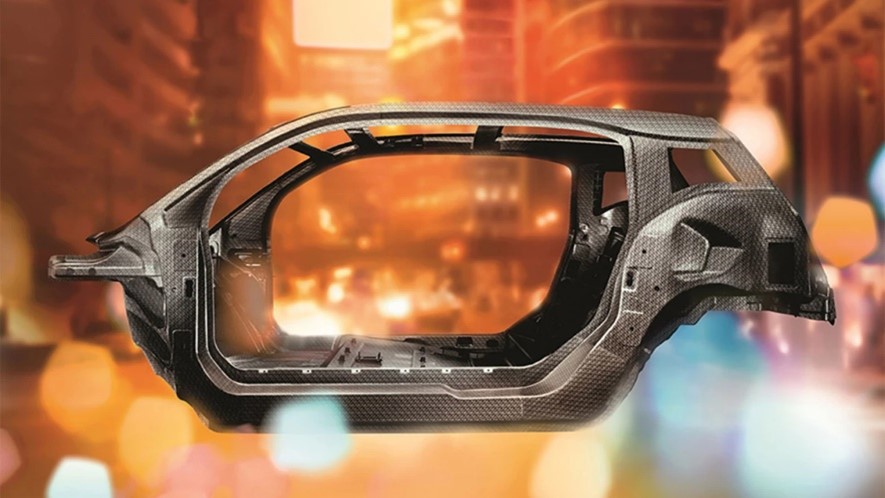
discover.bmw.co.uk
(Source: https://discover.bmw.co.uk/article/bmw-i3-naturally-charged)
Living in a Material World
When it comes to material choice, steel has typically been used for structural, powertrain and body parts in off-highway. It’s cheap, hard-wearing, easy to form and can be repaired easily. However, there are a range of different materials that are staring to gain traction as they support either better fuel efficiency or improved operational performance.
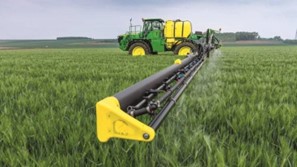
www.globalagtechinitiative.com
(Source: https://www.globalagtechinitiative.com/market-watch/john-deere-to-acquire-carbon-fiber-boom-manufacturer-in-spain/)
John Deere uses carbon fibre for its sprayer booms as opposed to steel. In some instances, it is nearly 1 tonne lighter than its steel equivalent. This helps to reduce weight and fuel usage. It also means a sprayer can be larger, reducing the number of passes a tractor must make to cover a field, further reducing the amount of fuel used.
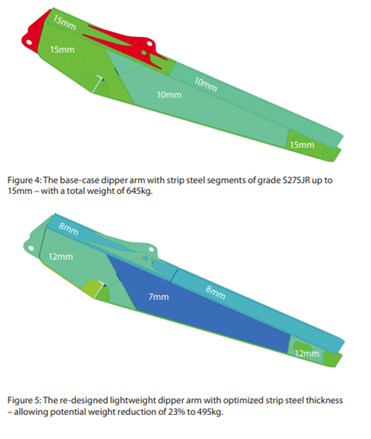
www.tatasteeleurope.com
(Source: https://www.tatasteeleurope.com/sites/default/files/tata-steel-engineering-ympress-s700mc-excavator-arm-high-strength-lightweight-datasheet-en-eu.pdf)
Tata Steel has simulated the use of its high-strength steel as a replacement material in excavator arms. A 23% weight reduction was achieved, saving both material costs and also meaning that either fuel is saved, or an excavator can move more material per cycle. This then boosts the operational performance of machine, positively impacting the bottom line of the mine or building contractor.
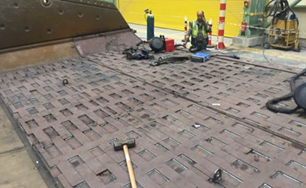
www.ssab.com
(Source: https://www.ssab.com/en/brands-and-products/hardox/customer-cases/2021/antech-attachments)
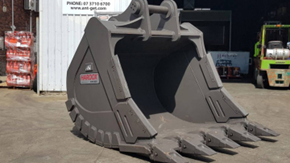
www.hardoxwearparts.com
(Source: https://www.hardoxwearparts.com/en/ssab-cases/haul-truck-body-dead-bed-with-longer-service-life)
Hardox – a steel product developed by SSAB AB – is wear resistant. It has been used in haul truck beds and in excavator buckets. Because of its hardness, less material is needed, making the parts lighter. In the case of the excavator bucket, a 30% reduction in weight is acheivable with a corresponding 20% increase in the amount of material that can be carried.
Simulation
Generative design is a software tool that allows components or parts to be designed that minimize material use whilst maximizing structural performance. Often looking “organic”, these new parts are iterated over thousands of generations from a starting design that is constrained by certain design parameters. This technique is becoming more common place in automotive, but it has the potential to revolutionize the design of off-highway machinery.
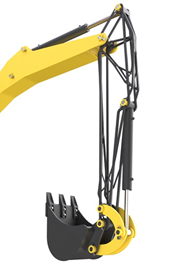
www.korall.io
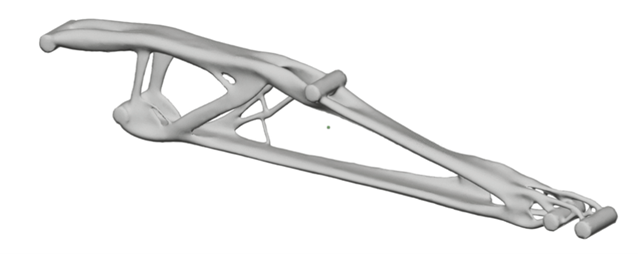
www.korall.io
(Source: https://www.korall.io/projects-jhondeere.html)
Korall Engineering used generative design to reduce the weight of a John Deere excavator boom. The final topology optimised design shows a 13.3% reduction in mass by comparison with the original arm design: this product is about 90Kg lighter. The generative design shows a 56.2% reduction in mass by comparison with the original arm design: this product is about 380Kg lighter.
Weighing Up
Ukraine- and COVID-related supply chain issues won’t abate soon. It’s also entirely likely that there will be other flash points in coming years that impact global supply chains, particularly with the substantial transitions away from fossil fuels to energy technologies that require multiple, rare-earth materials.
To protect against material shortages (and energy price fluctuations) then OEMs would be well advised to investigate how they can use less material and how they can integrate materials that are less likely to be in short-term demand. The benefit to this approach is that it means that OEMs can protect against future price increases (which usually get passed on to customers) and also guarantee product availability, which is likely to be a competitive advantage for some time.
Use of simulation and different materials could significantly reduce the weight of certain components. In the case of excavator arms, this could be deployed on both new AND existing machines. This is a fundamental game changer as the fuel/operational efficiency of machines currently in the market is not something that can easily be changed.
Perhaps the biggest reason to look at materials, particularly lightweight materials, is the shift to electric machinery. Reducing the weight of electric machines will help to extend the operational performance of the battery or help reduce the size of battery needed. This either improves customer performance or brings the price of the machine down.
It is high time that the off-highway market looked again at the materials it uses in machines and identifies ways to reduce the amount it uses.
For more information, please contact Senior Research Director Alastair Hayfield: alastair.hayfield@interactanalysis.com
其他商用车领域洞察